Our projects tell of innovative solutions, technical expertise and partnership-based cooperation. Each reference stands for individual challenges and customized results that create real added value. Discover a selection of success stories that demonstrate our commitment and expertise.
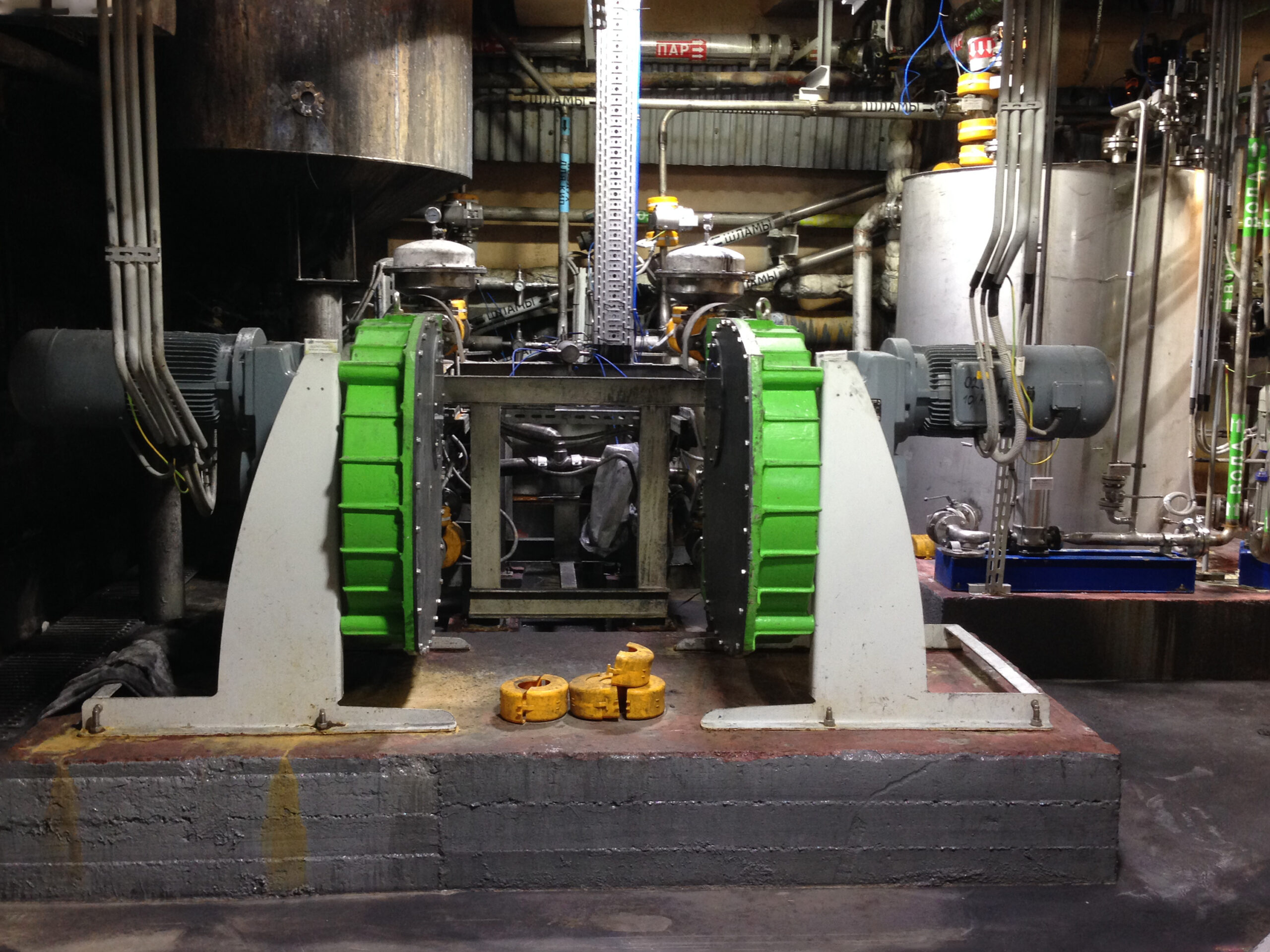
Modernization of an electrolysis department and fully automated PGM sludge processing
MMC Norilsk Nickel intended to comprehensively modernize its electrolysis department at the copper plant and build a state-of-the-art plant for processing precious metal-containing anode slimes (PGM sludge). The aim was to achieve maximum efficiency and product purity at every stage of the process.
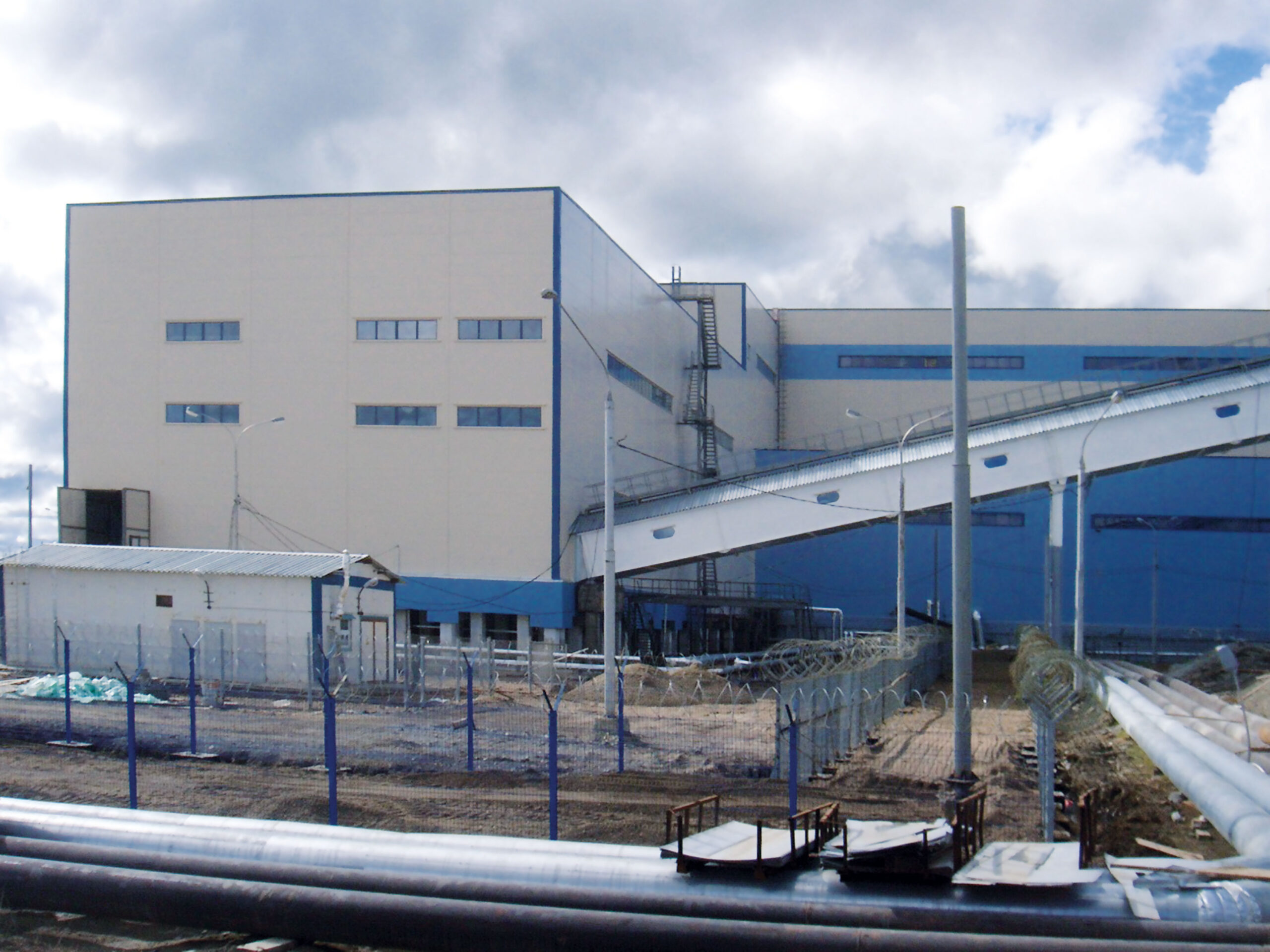
3-stage sludge dewatering and drying line
The Mirny diamond mine operates in a permafrost area with frozen ground all year round. Phase 1 already showed that the annual sludge volumes exceeded the available landfill sites. The aim of both project phases was to drastically reduce the landfill area, increase the internal water cycle to over 95 % and keep residual moisture in the filter cake below 25% – all without interrupting ongoing operations.
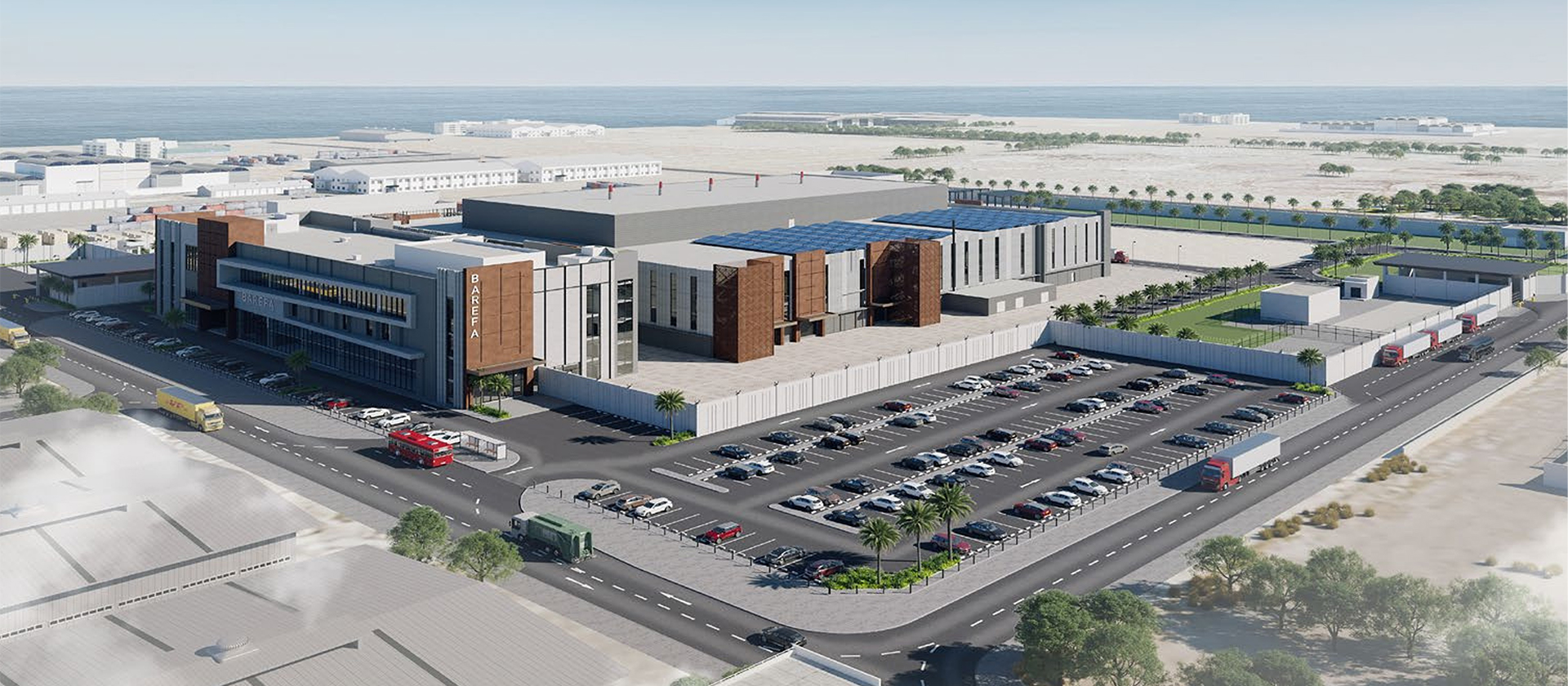
Pre-FEED study of a PGM refinery
The customer planned to build a state-of-the-art PGM refinery to process a metal-rich concentrate. The aim was to achieve an outstanding precious metal yield with maximum product purity in a single step. At the same time, environmental requirements were to be taken into account and energy consumption reduced to a minimum.
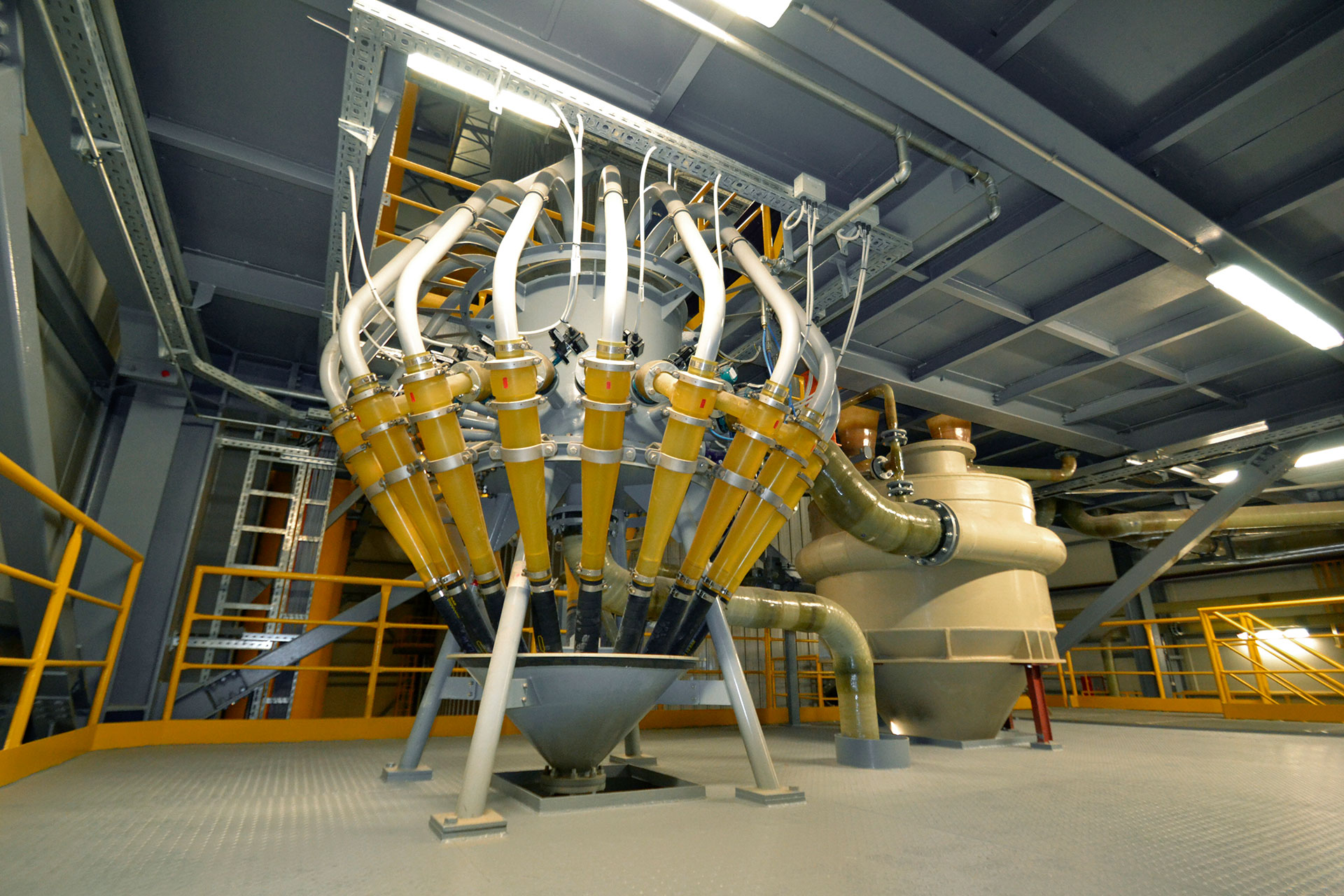
Flue gas desulphurization system
State-of-the-art environmental technology for sustainable energy: our flue gas desulphurization plant at the Šoštanj power plant ensures a significant reduction in sulphur emissions and meets the highest environmental standards.
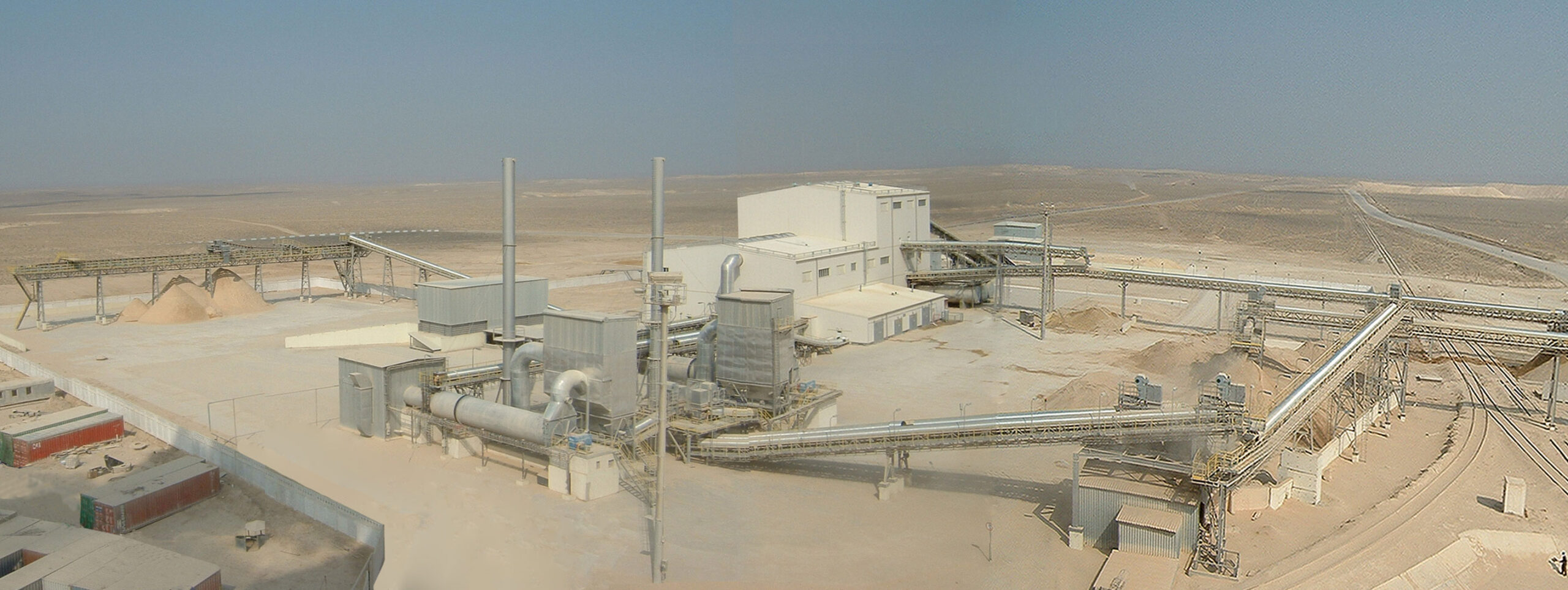
Phosphate treatment plant & calcination plant
Efficient phosphate ore processing in Uzbekistan: Following the successful commissioning of the phosphate processing plant at the "Tashkura I" deposit, we increased production capacity by 52 t/h with the construction of the calcination plant at the "Tashkura II" deposit and set new standards in the use of resources and technological development.
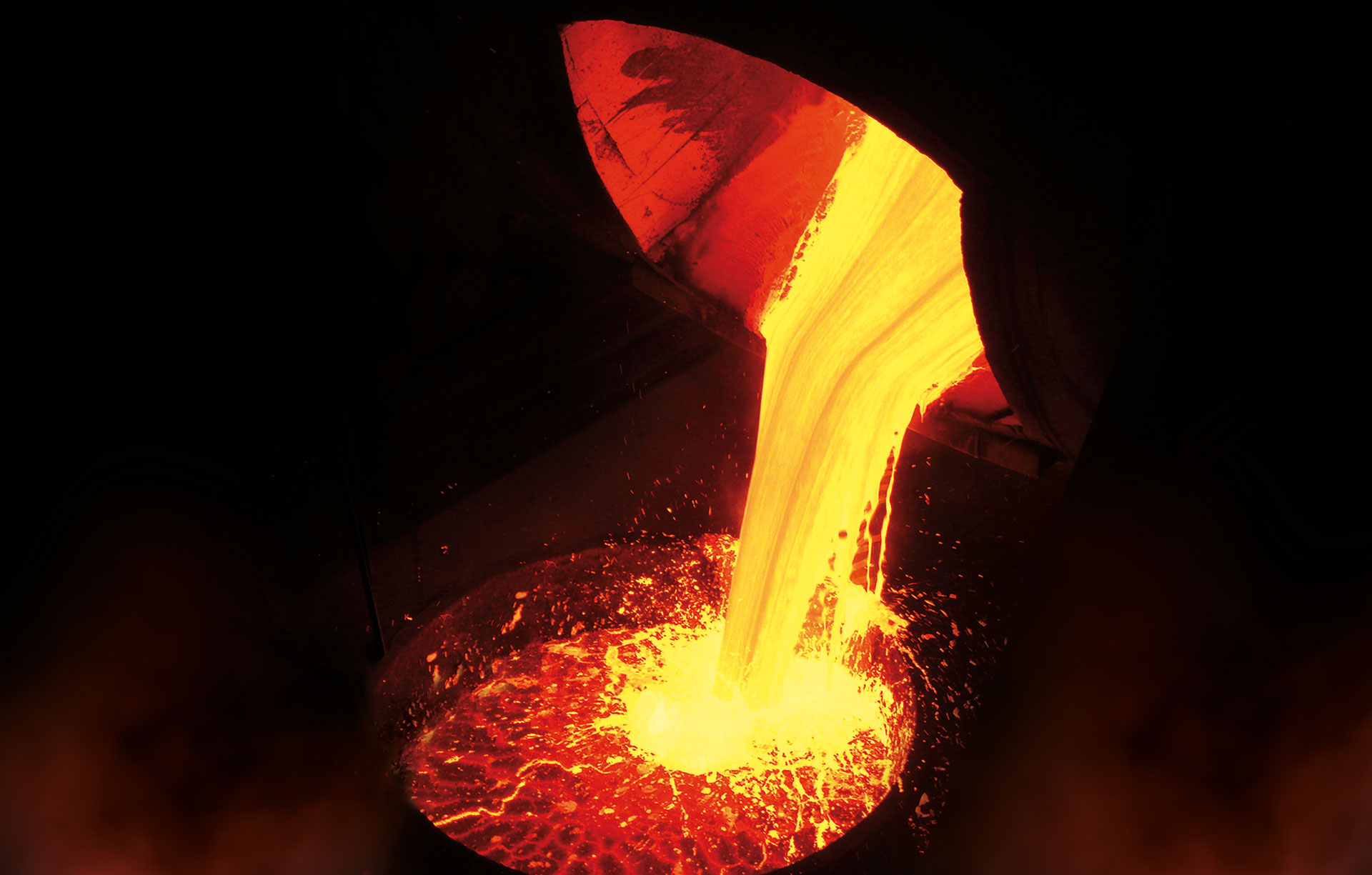
Copper smelter & lead works
Modernized copper and lead production in Kazakhstan: We have built a copper smelter with electrolysis and an expanded lead plant for Kazzinc Ltd. to increase production capacity to 87,500 tonnes of copper and 100,000 tonnes of lead per year and improve the environmental footprint through innovative technologies.
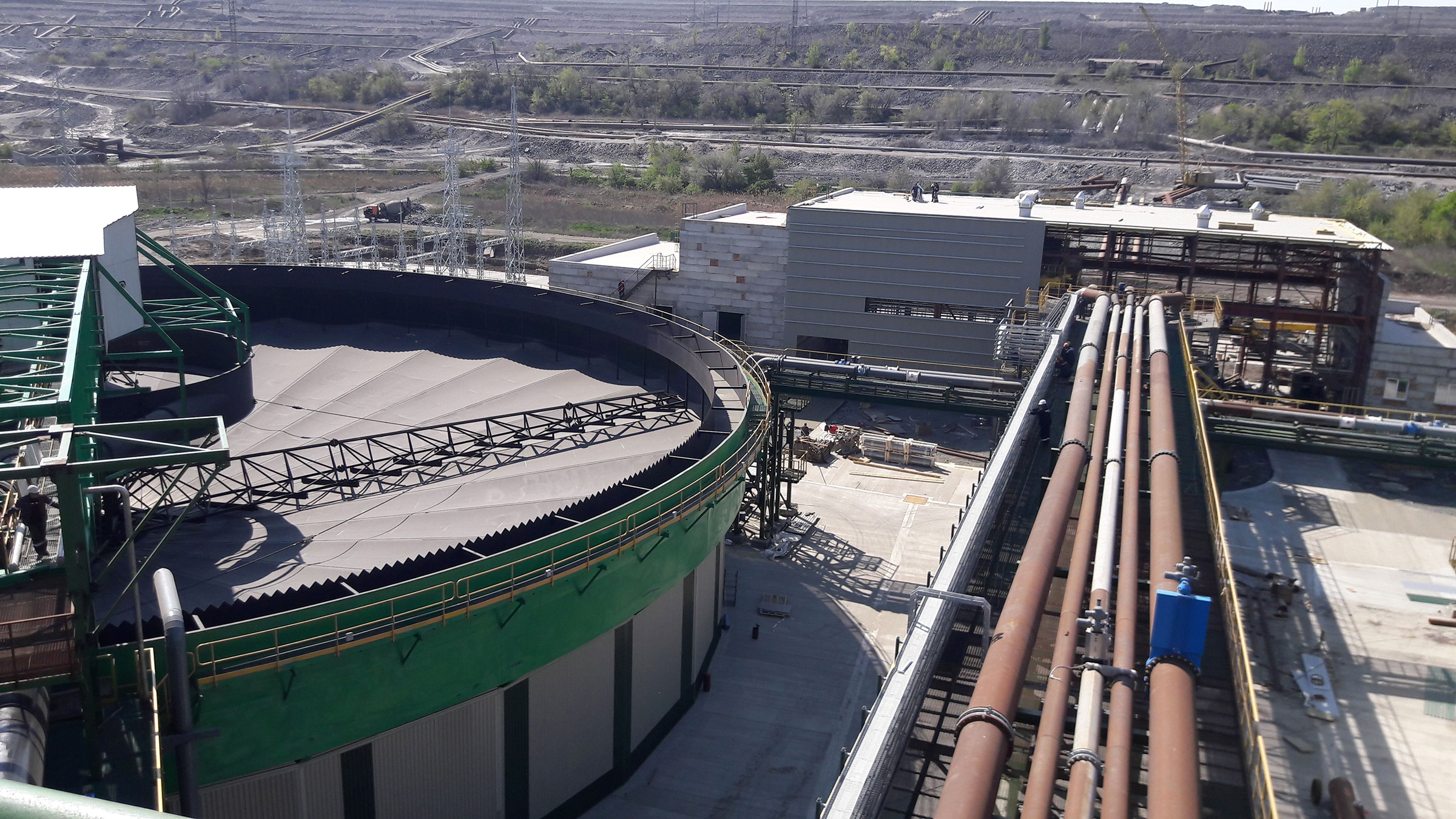
Thickening plant
Sustainable innovation for iron ore in Ukraine: With a state-of-the-art thickening plant, we are improving processing capacity for UGOK and significantly reducing the environmental impact through efficient process water treatment and waste minimization.
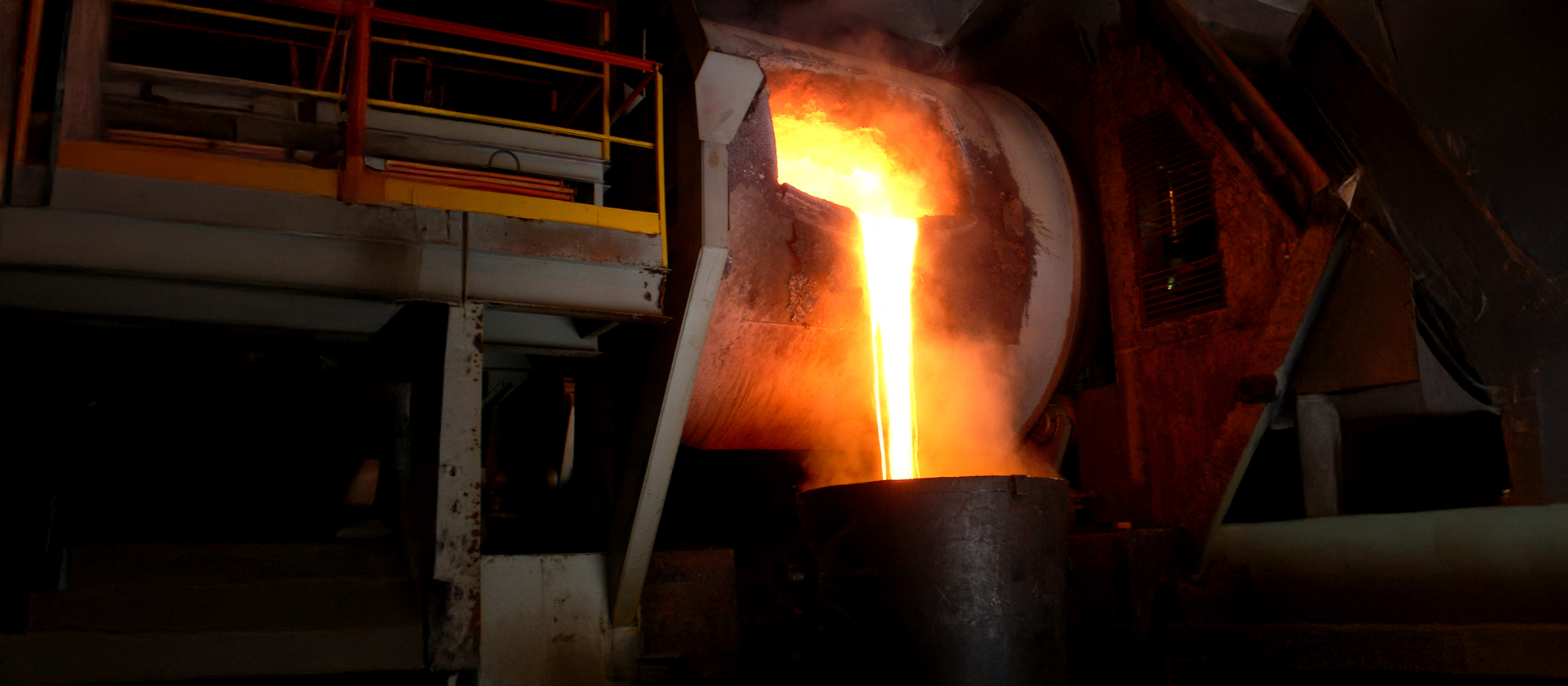
Copper smelter / Vanyukov furnace
Efficient copper production in Almalyk: With the innovative Vanjukov furnace, we enable an annual production of 73,800 tons of blister copper for JSC Almalyk MMC and improve both the production output and the environmental balance thanks to modern slag bath technology.
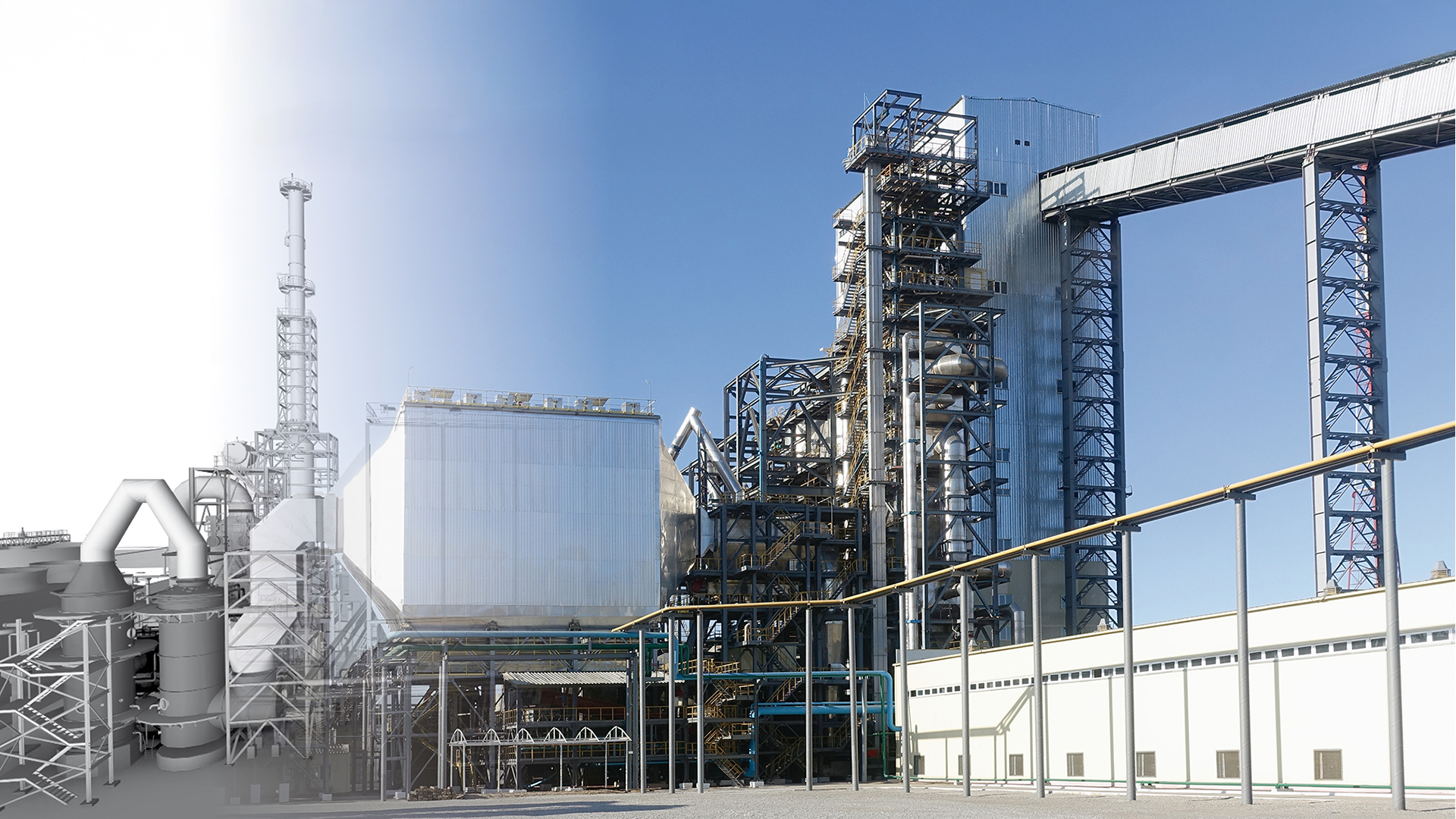
Roasting plant
Globally unique STR system for gold extraction in Uchquduq: With the innovative roasting plant, we are increasing raw material efficiency for NGMK by 8% and setting new standards in the processing of refractory ores with a capacity of up to 83 tons/hour.
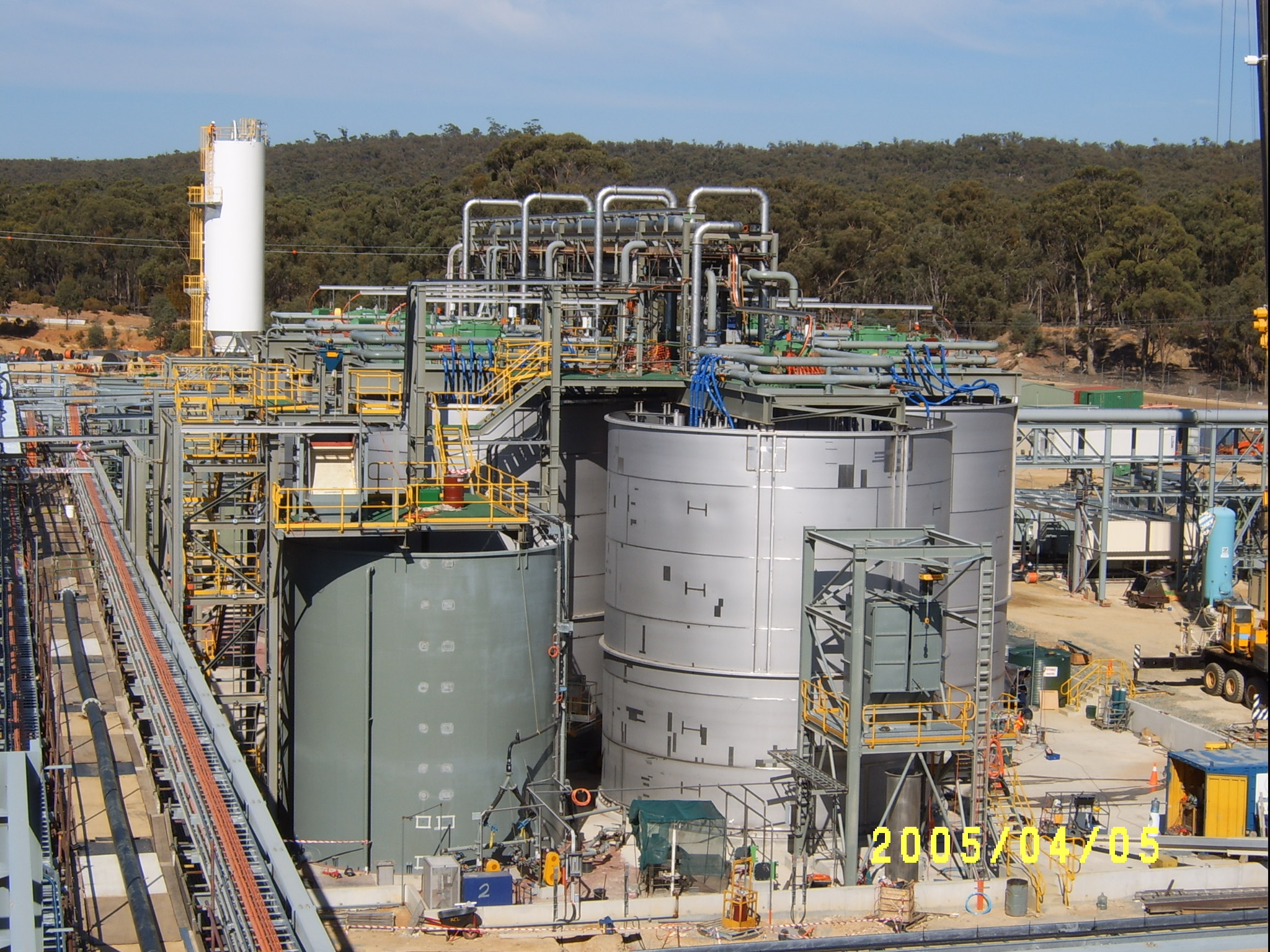
Gold extraction plant for complex ores
State-of-the-art bio-oxidation technology for gold in Kokpatas, Uzbekistan: This highly innovative plant, which we developed together with Navoi Mining and Metallurgical Combine, processes 3.2 million tons of complex, sulphide ores annually and sets new standards in the efficiency and sustainability of gold extraction.
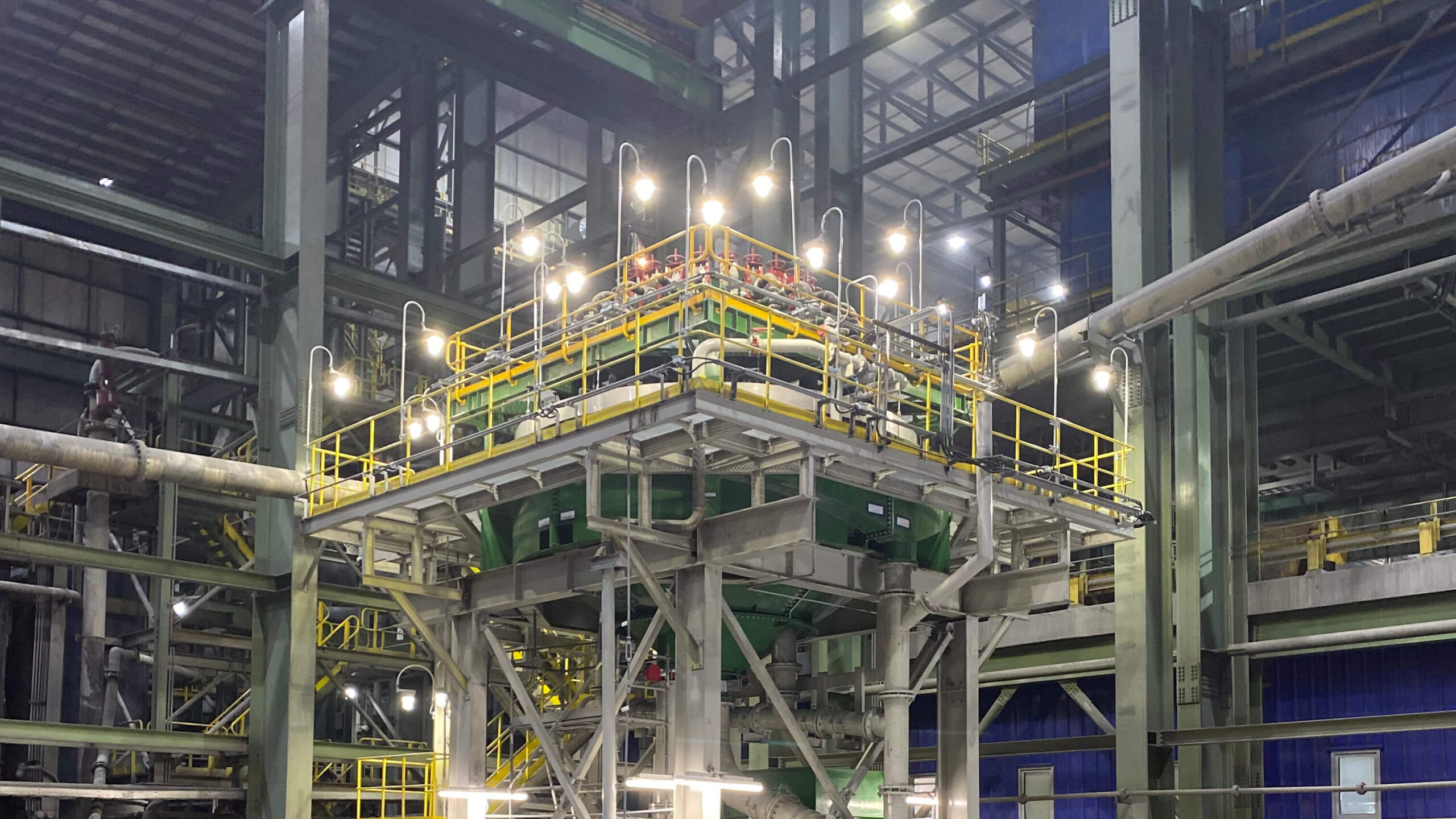
Flotation plant for sulphide processing
State-of-the-art flotation technology for Central Asia: We have developed a flotation plant that raises sulphide processing to a new level of efficiency with an impressive capacity of 3500 t/h.
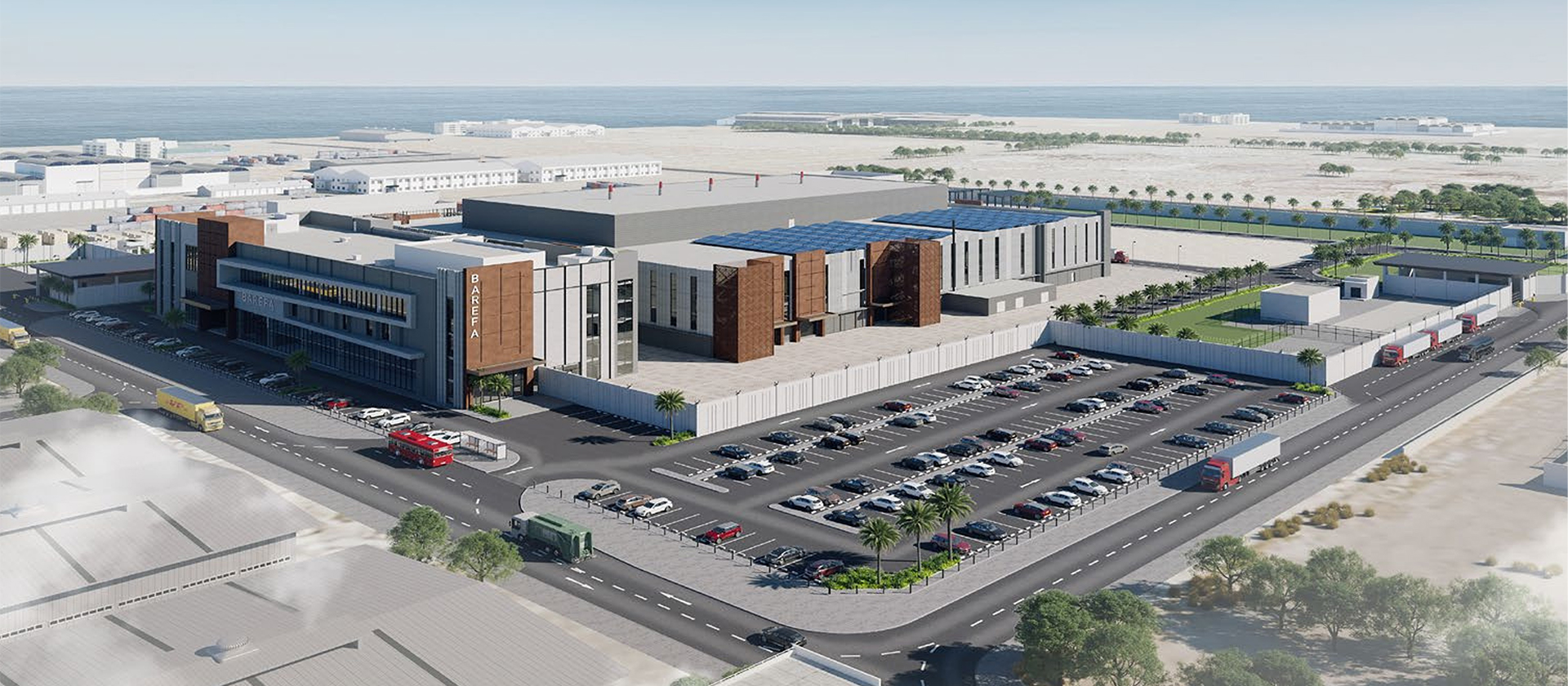
Pre-FEED study of a PGM refinery
The customer planned to build a state-of-the-art PGM refinery to process a metal-rich concentrate. The aim was to achieve an outstanding precious metal yield with maximum product purity in a single step. At the same time, environmental requirements were to be taken into account and energy consumption reduced to a minimum.
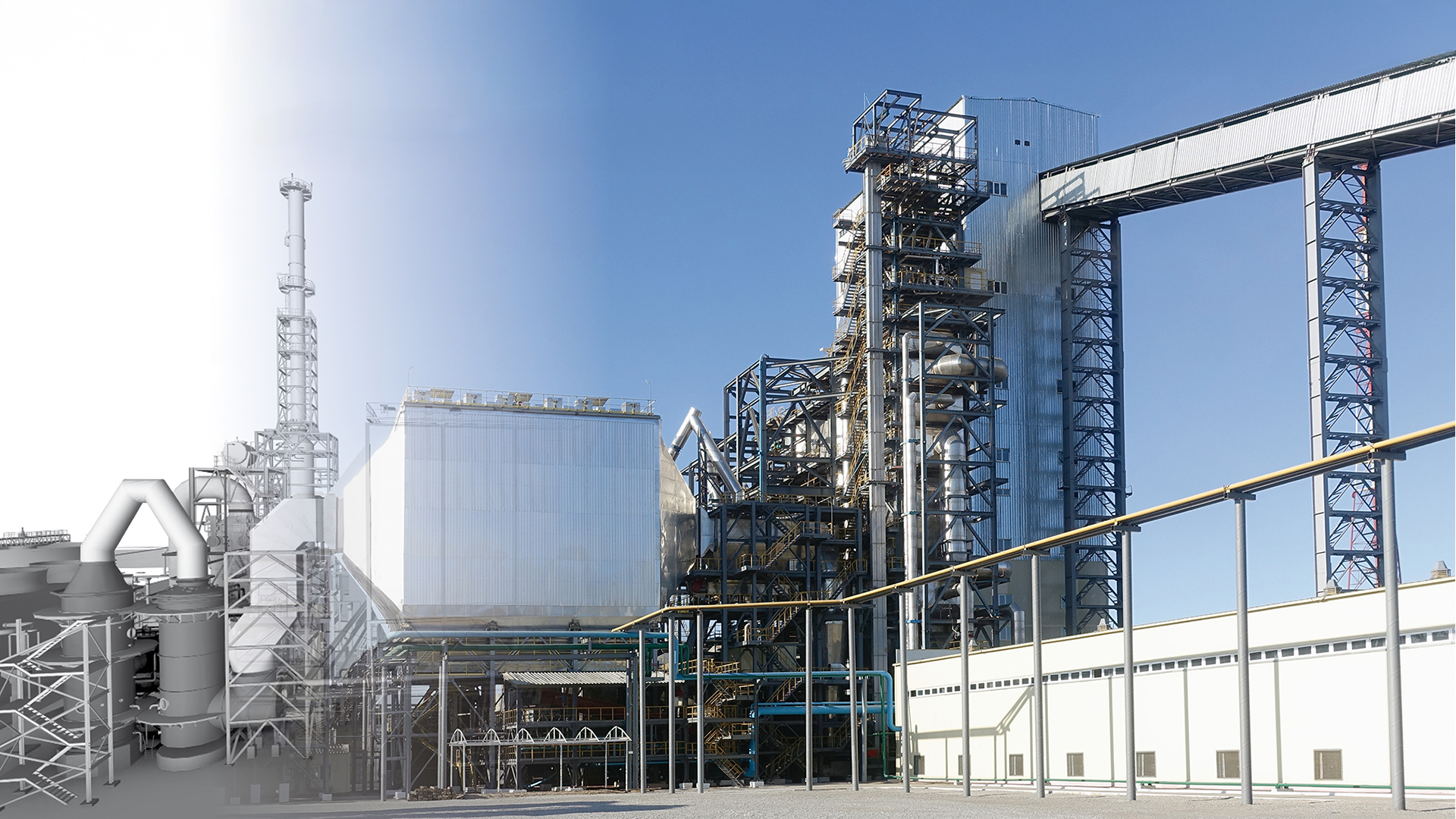
Roasting plant
Globally unique STR system for gold extraction in Uchquduq: With the innovative roasting plant, we are increasing raw material efficiency for NGMK by 8% and setting new standards in the processing of refractory ores with a capacity of up to 83 tons/hour.
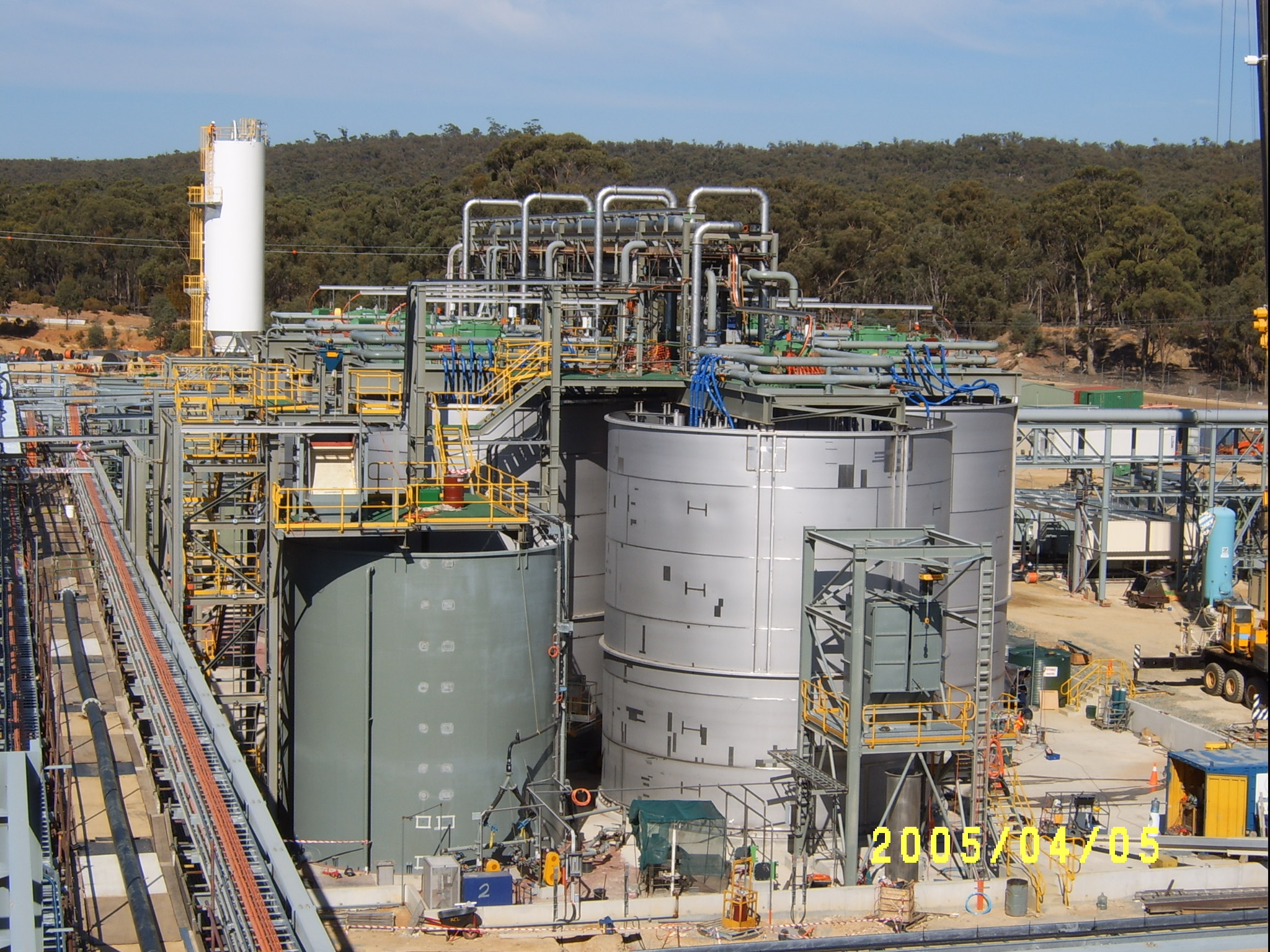
Gold extraction plant for complex ores
State-of-the-art bio-oxidation technology for gold in Kokpatas, Uzbekistan: This highly innovative plant, which we developed together with Navoi Mining and Metallurgical Combine, processes 3.2 million tons of complex, sulphide ores annually and sets new standards in the efficiency and sustainability of gold extraction.
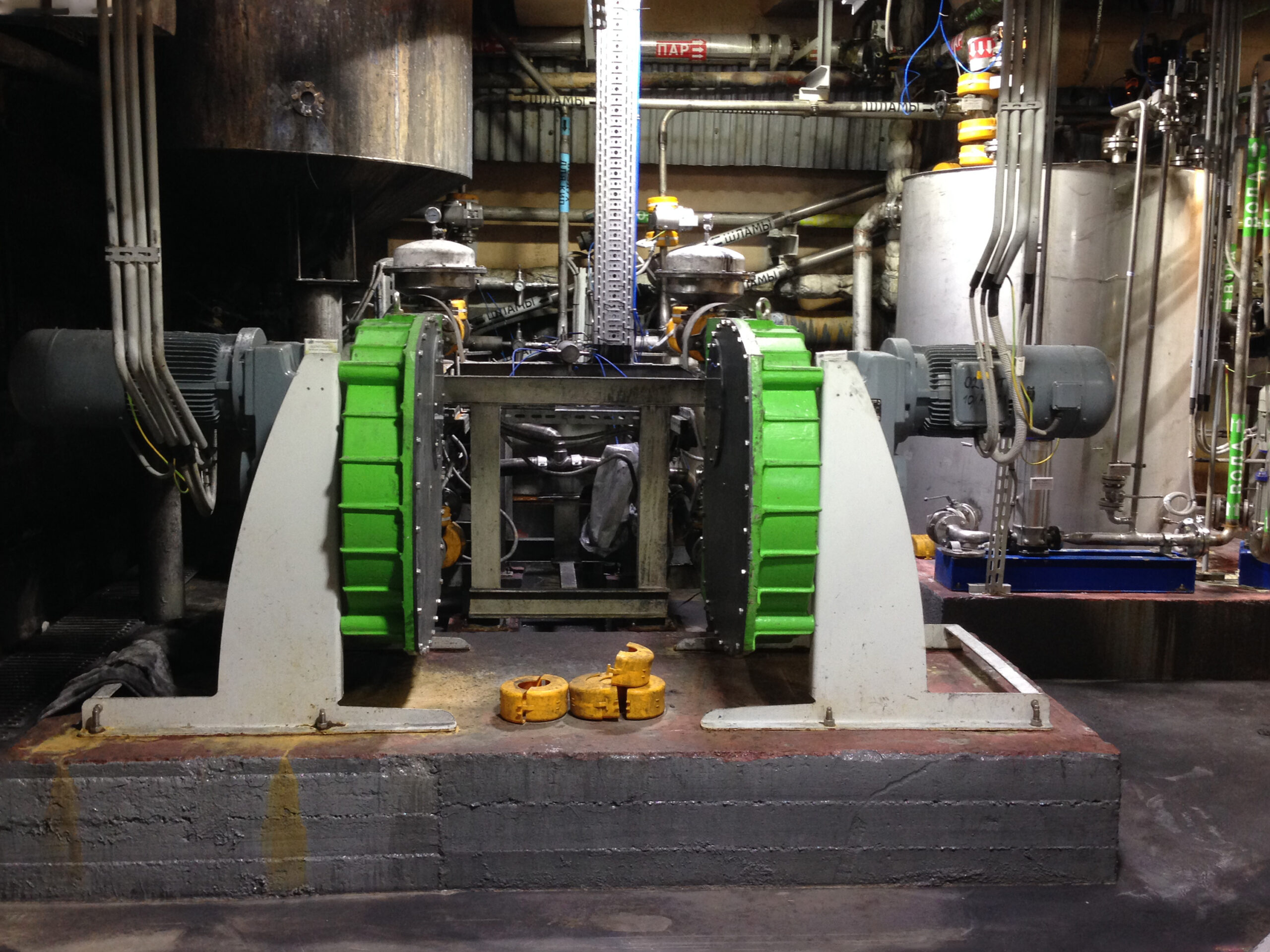
Modernization of an electrolysis department and fully automated PGM sludge processing
MMC Norilsk Nickel intended to comprehensively modernize its electrolysis department at the copper plant and build a state-of-the-art plant for processing precious metal-containing anode slimes (PGM sludge). The aim was to achieve maximum efficiency and product purity at every stage of the process.
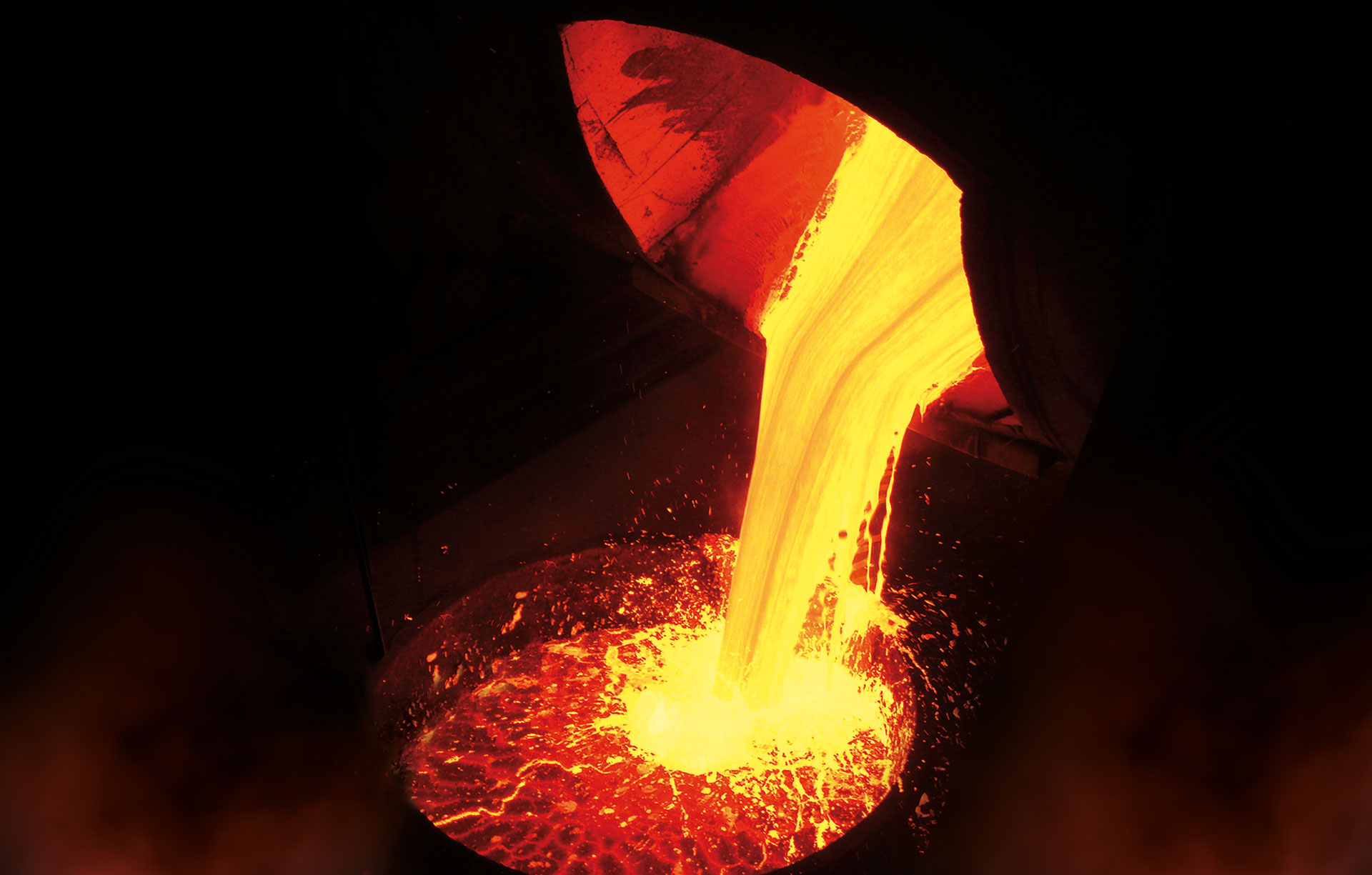
Copper smelter & lead works
Modernized copper and lead production in Kazakhstan: We have built a copper smelter with electrolysis and an expanded lead plant for Kazzinc Ltd. to increase production capacity to 87,500 tonnes of copper and 100,000 tonnes of lead per year and improve the environmental footprint through innovative technologies.
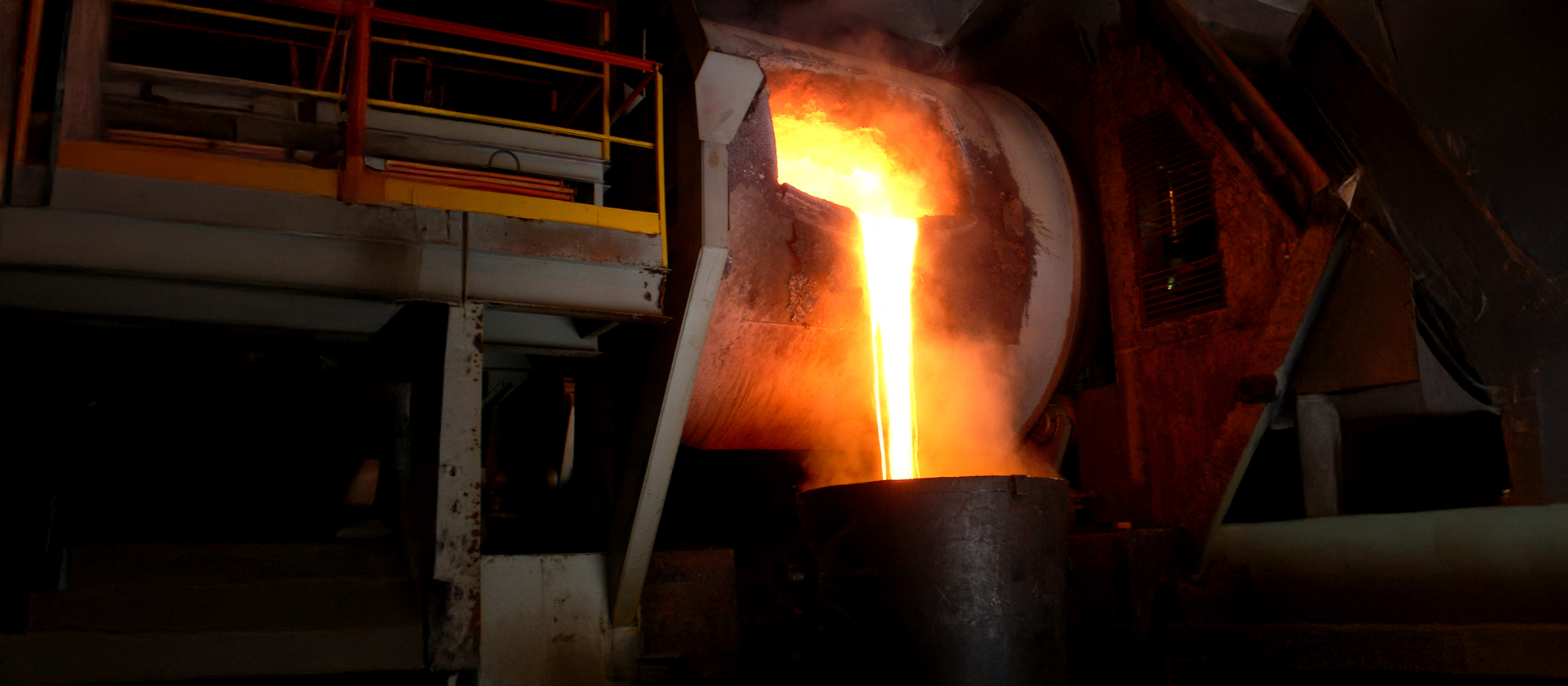
Copper smelter / Vanyukov furnace
Efficient copper production in Almalyk: With the innovative Vanjukov furnace, we enable an annual production of 73,800 tons of blister copper for JSC Almalyk MMC and improve both the production output and the environmental balance thanks to modern slag bath technology.
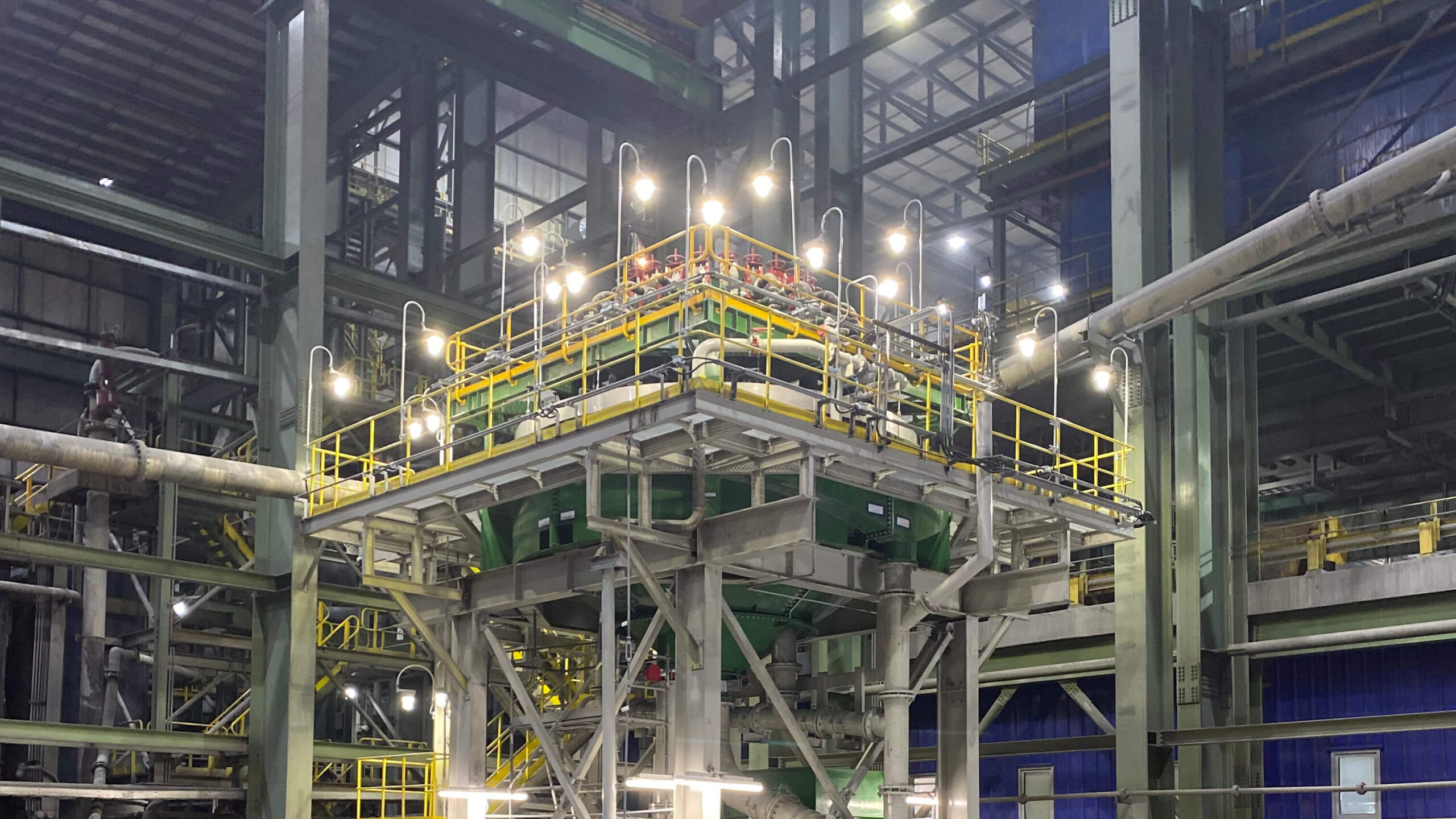
Flotation plant for sulphide processing
State-of-the-art flotation technology for Central Asia: We have developed a flotation plant that raises sulphide processing to a new level of efficiency with an impressive capacity of 3500 t/h.
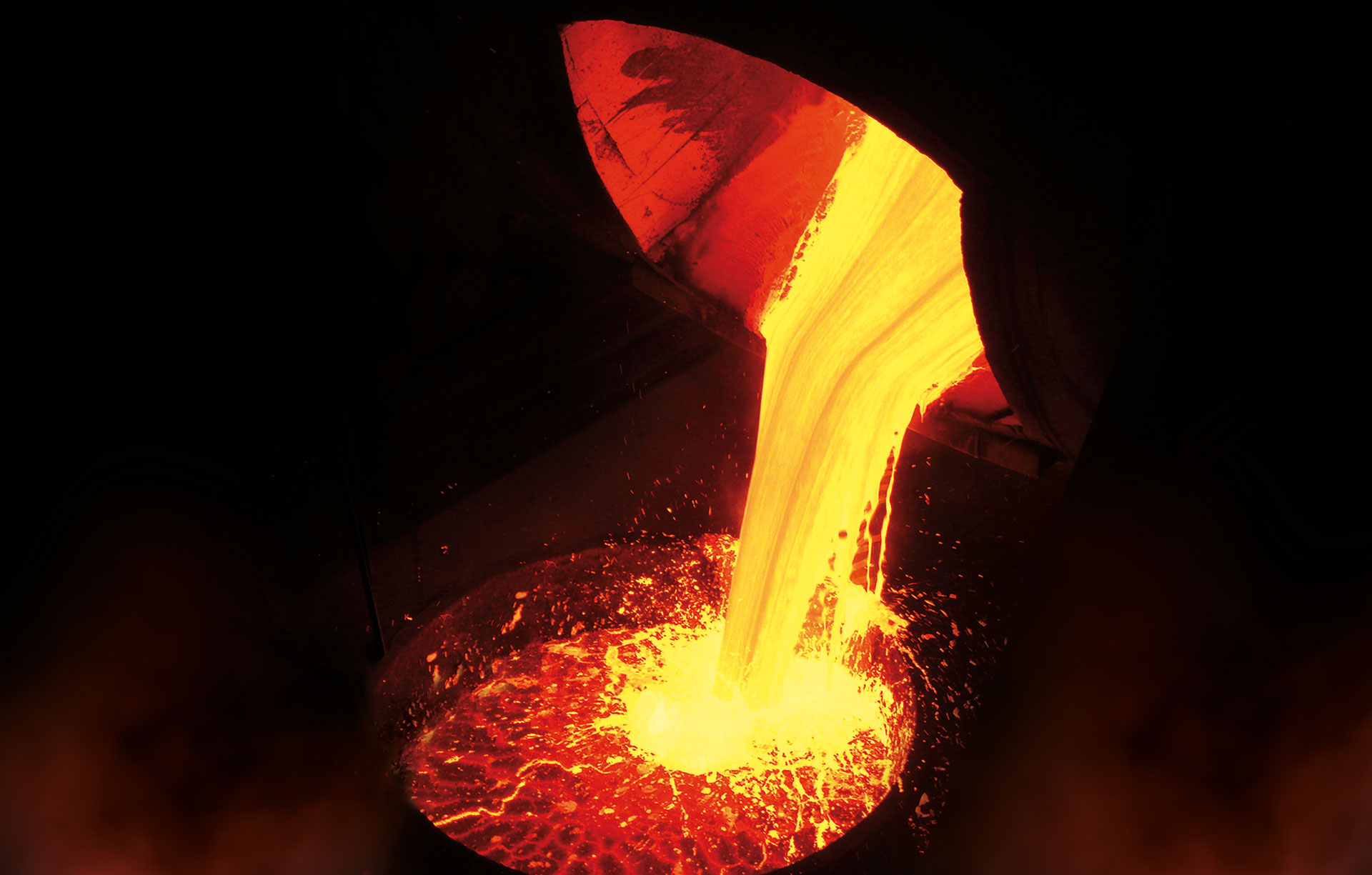
Copper smelter & lead works
Modernized copper and lead production in Kazakhstan: We have built a copper smelter with electrolysis and an expanded lead plant for Kazzinc Ltd. to increase production capacity to 87,500 tonnes of copper and 100,000 tonnes of lead per year and improve the environmental footprint through innovative technologies.
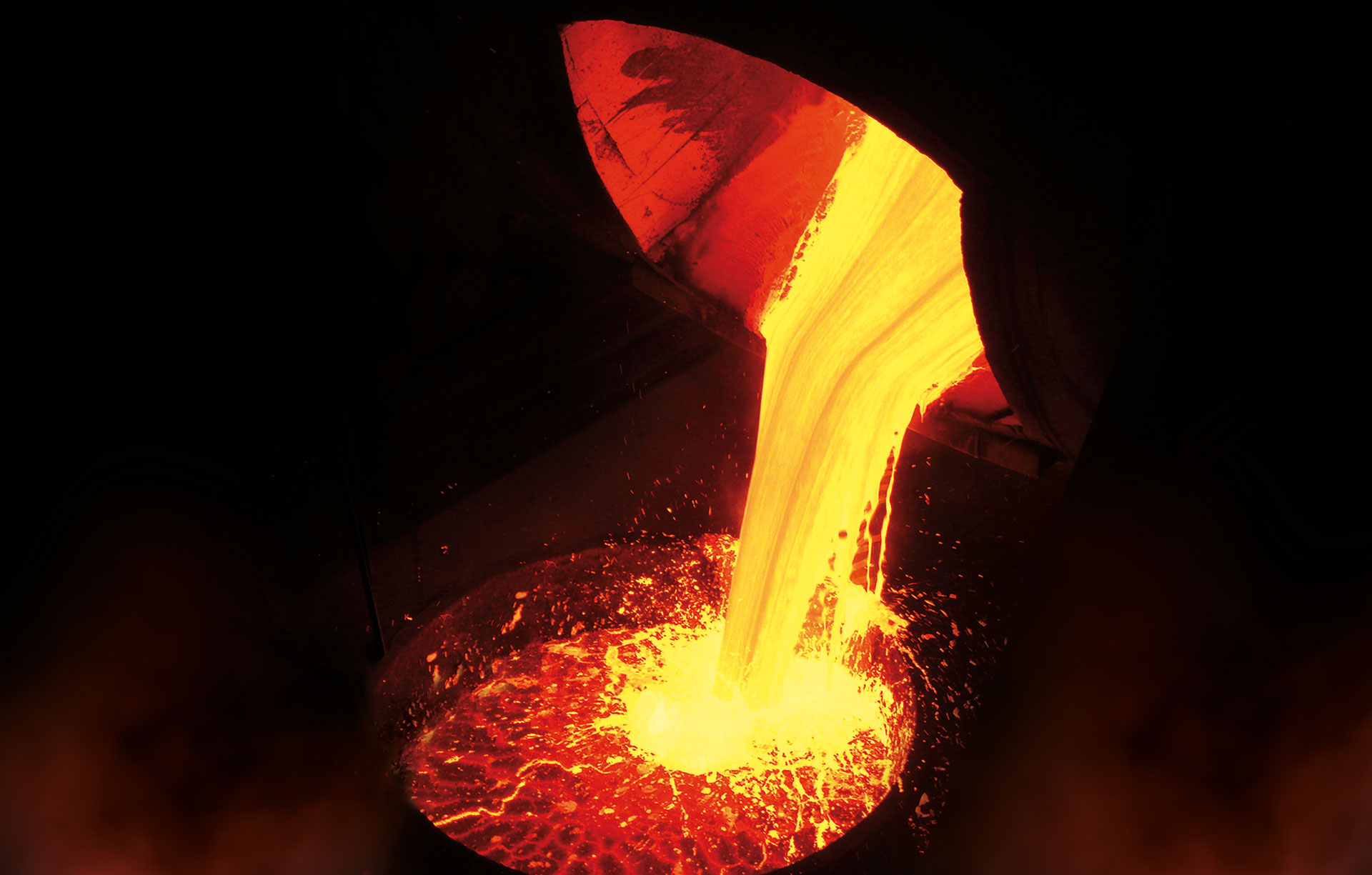
Copper smelter & lead works
Modernized copper and lead production in Kazakhstan: We have built a copper smelter with electrolysis and an expanded lead plant for Kazzinc Ltd. to increase production capacity to 87,500 tonnes of copper and 100,000 tonnes of lead per year and improve the environmental footprint through innovative technologies.
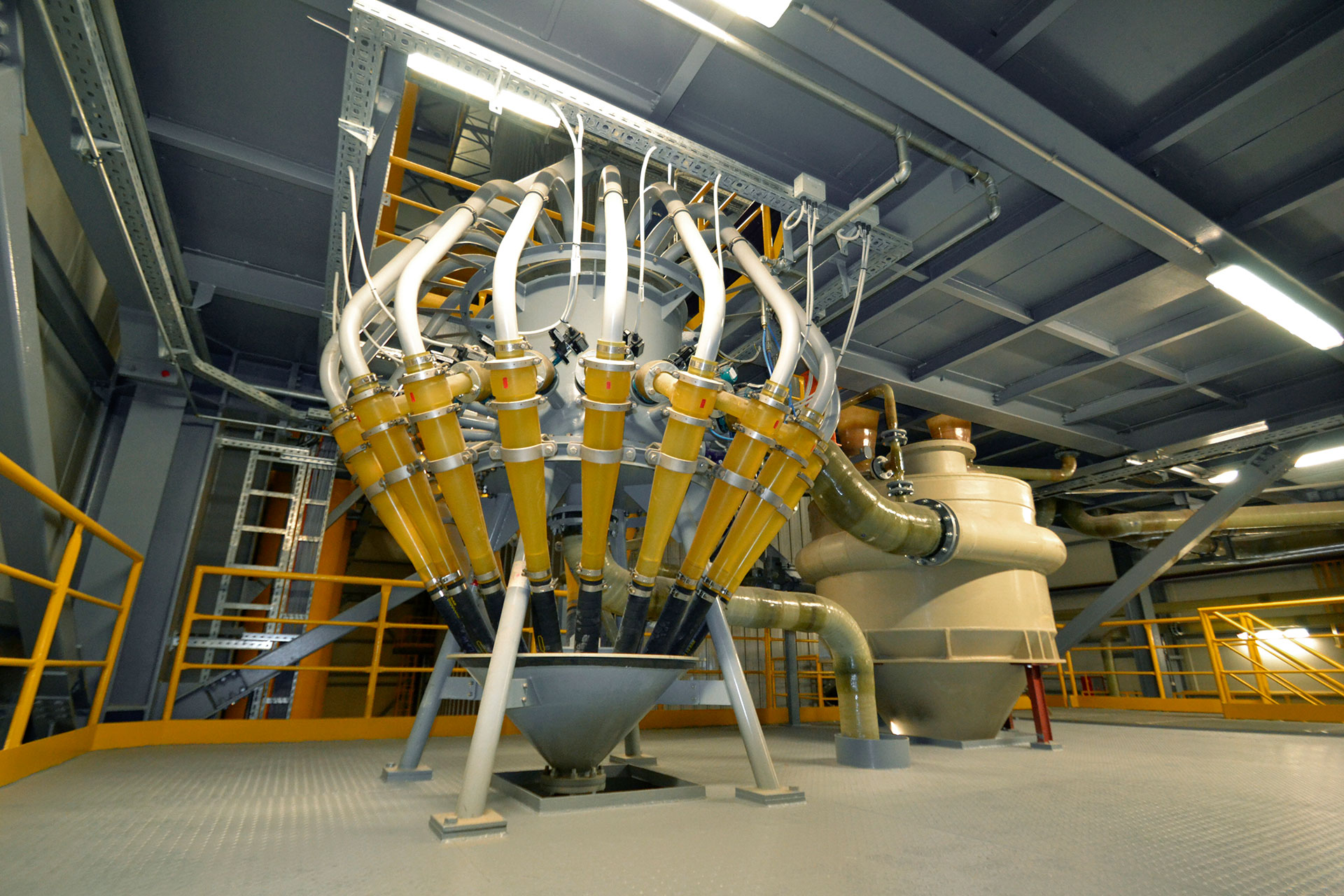
Flue gas desulphurization system
State-of-the-art environmental technology for sustainable energy: our flue gas desulphurization plant at the Šoštanj power plant ensures a significant reduction in sulphur emissions and meets the highest environmental standards.
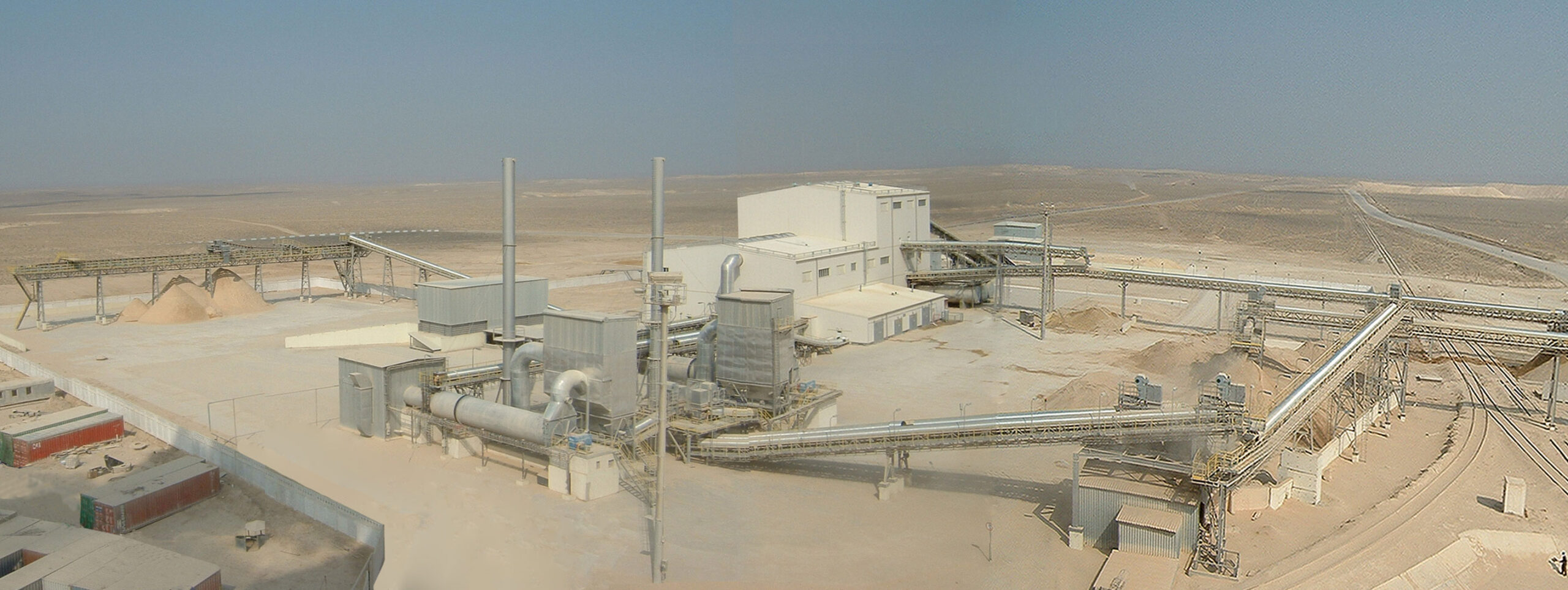
Phosphate treatment plant & calcination plant
Efficient phosphate ore processing in Uzbekistan: Following the successful commissioning of the phosphate processing plant at the "Tashkura I" deposit, we increased production capacity by 52 t/h with the construction of the calcination plant at the "Tashkura II" deposit and set new standards in the use of resources and technological development.
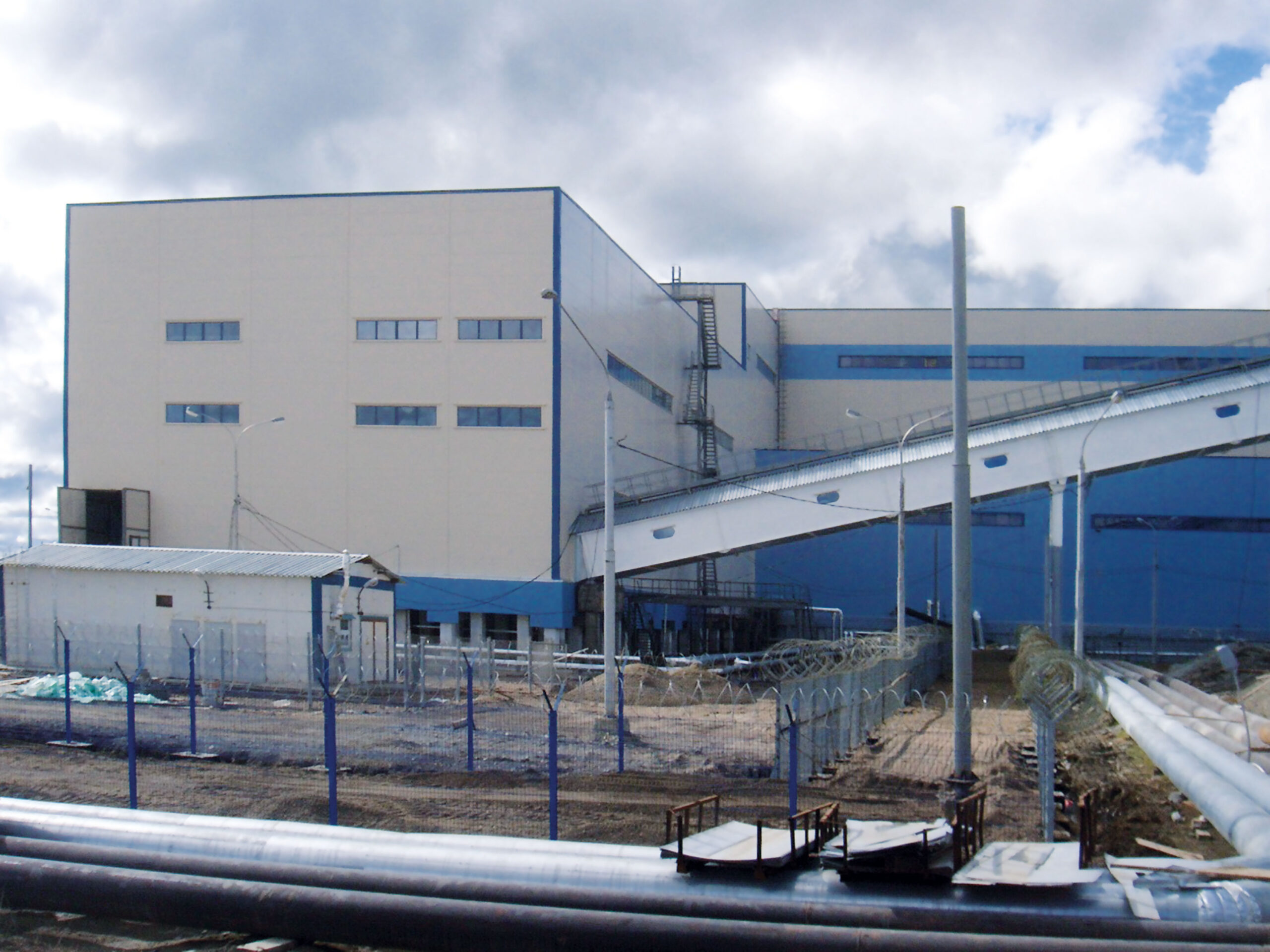
3-stage sludge dewatering and drying line
The Mirny diamond mine operates in a permafrost area with frozen ground all year round. Phase 1 already showed that the annual sludge volumes exceeded the available landfill sites. The aim of both project phases was to drastically reduce the landfill area, increase the internal water cycle to over 95 % and keep residual moisture in the filter cake below 25% – all without interrupting ongoing operations.